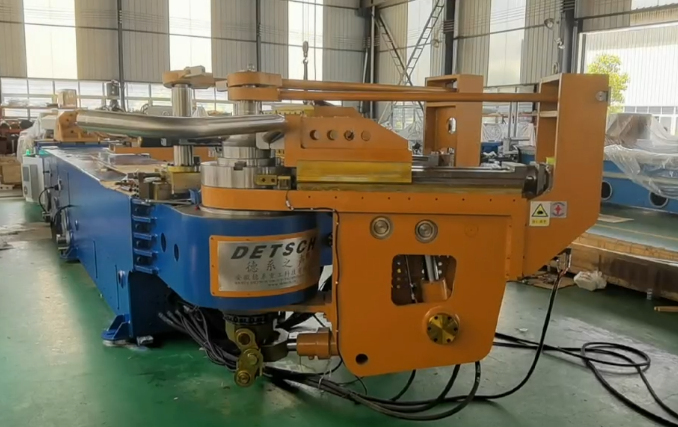
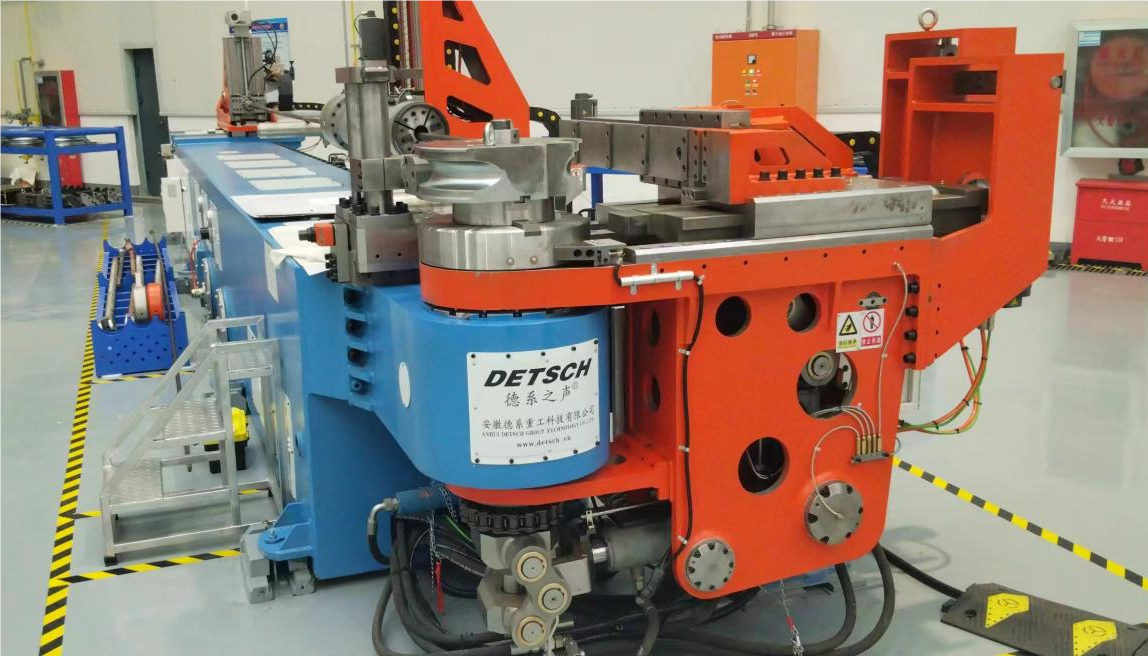
高端数控弯管机
DETSCH 140CNC 技术方案
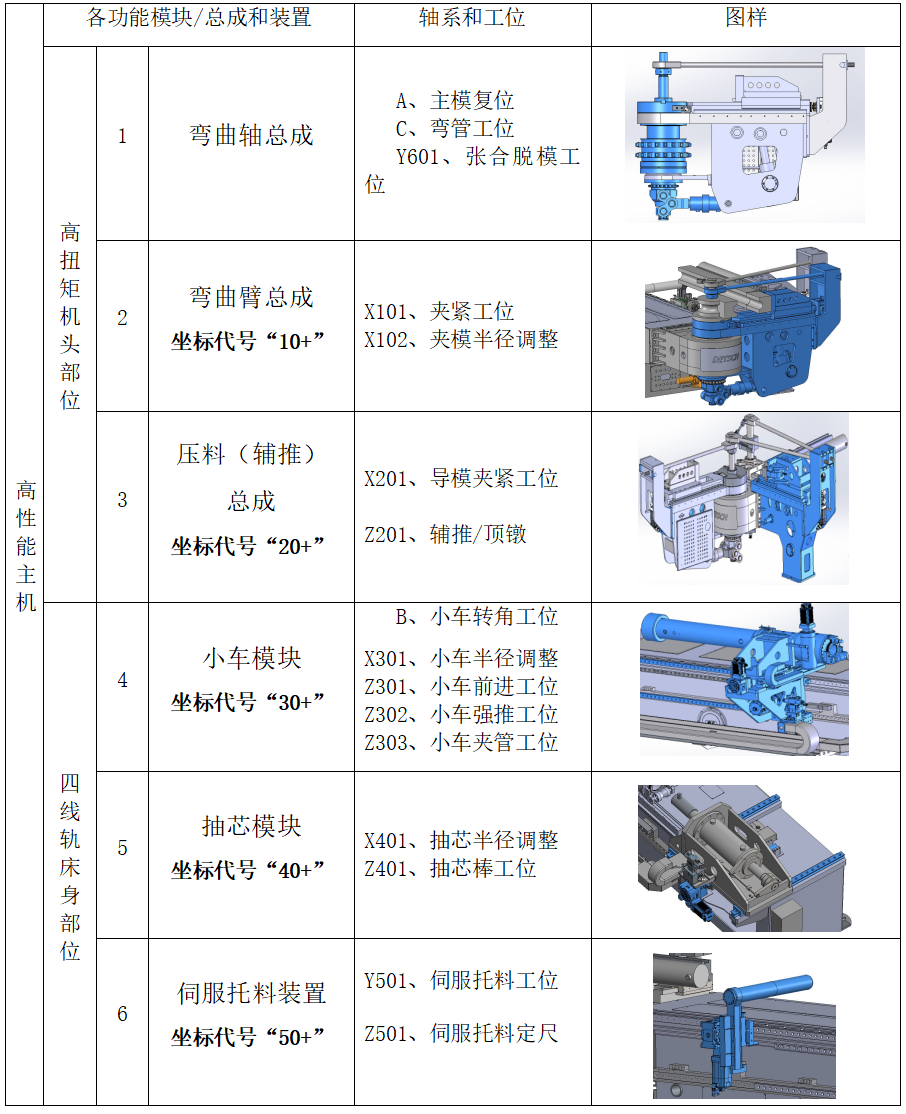
2.高性能主机
由全球最高扭矩密度机头和高强度重载四线轨床身组成
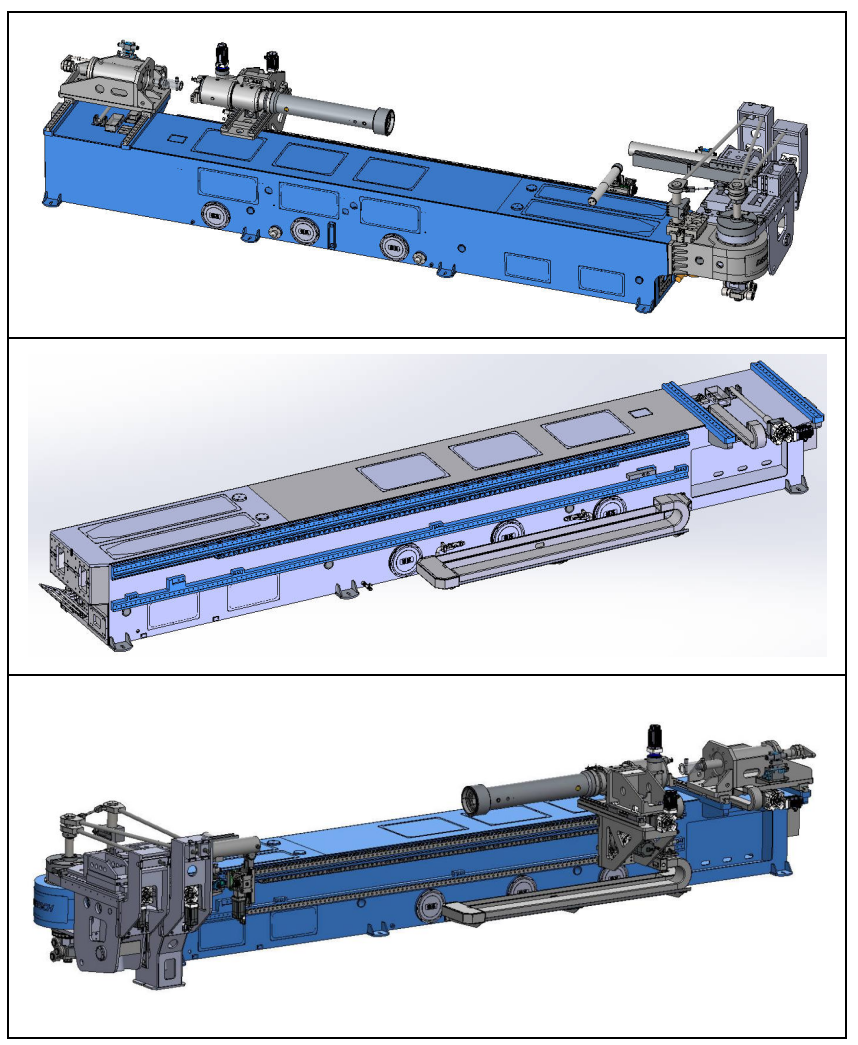
3.1.机头,兼顾左弯和右弯、短伸出对称式高功率密度设计,经有限元受力分析(FEM)和拓扑优化结构,采用高强度低合金板材加热焊接而成,并经退火和抛丸处理消除内应力防永久形变,机加工后机头在组装前安装面均经配研和铲刮工艺确保安装贴合精度和最低位置误差。
3.1.1.弯曲轴总成与弯曲臂总成连接,安装在机头内,获得最高扭矩度。
3.1.2.压料(辅推)模块安装在机头左侧或右侧,兼顾左弯或右弯(单层模)。
3.1.机头,兼顾左弯和右弯、短伸出对称式高功率密度设计,经有限元受力分析(FEM)和拓扑优化结构,采用高强度低合金板材加热焊接而成,并经退火和抛丸处理消除内应力防永久形变,机加工后机头在组装前安装面均经配研和铲刮工艺确保安装贴合精度和最低位置误差。
3.1.1.弯曲轴总成与弯曲臂总成连接,安装在机头内,获得最高扭矩度。
3.1.2.压料(辅推)模块安装在机头左侧或右侧,兼顾左弯或右弯(单层模)。
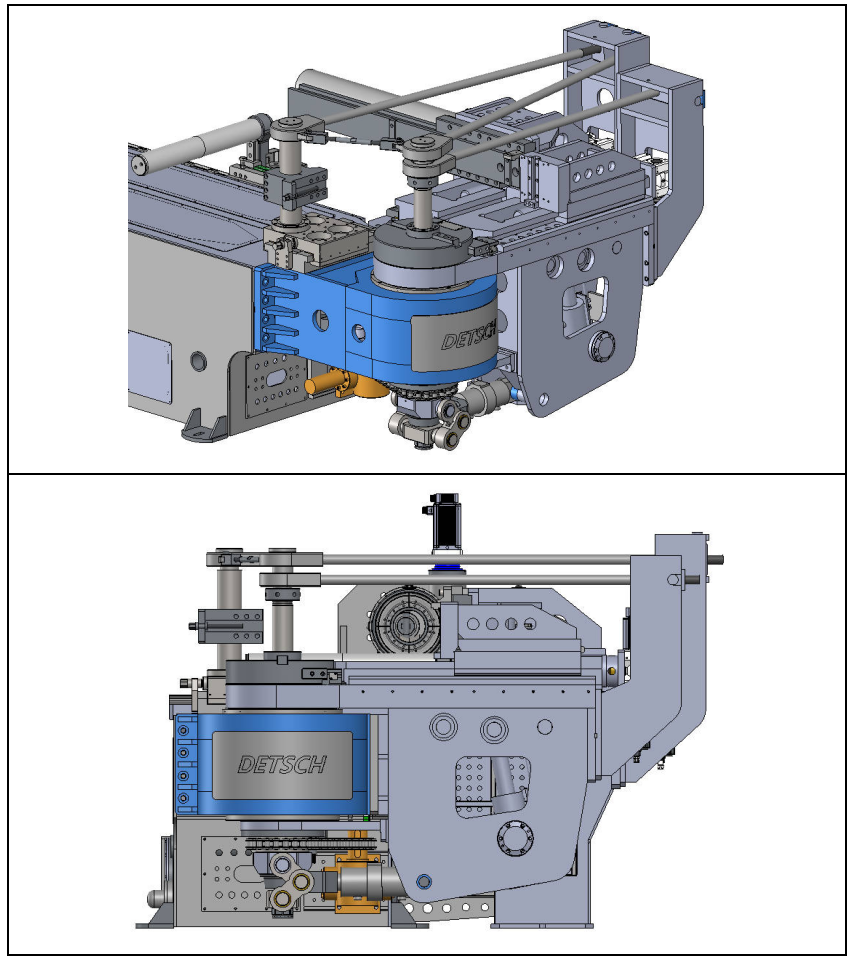
3.2.床身及导向装置,采用高强度低合金板材加热焊接而成保证足够的强度,重载四线轨布局,内置液压系统,经有限元受力分析(FEM)和拓扑优化,加强筋纵横交错并经退火和抛丸处理消除内应力,防止床身两侧呈90度分布的两根重载滚柱线轨在作业受力时的震动和变形。机加工后安装面均经配研和铲刮,最大程度的保障线轨安装精度和最低位置误差。
3.2.1.高强度高精度的床身特质,保障了床身上的两个模块(小车和伺服托料)高线性动态性能和刚度。床身侧面安装的滚柱线轨满足小车一次性行程6米。
3.2.2.油箱、电机油泵组及伺服液压系统均安装在床身内部,极大的减少了占地面积,床身上有多个观察窗口便于系统安装、维护。利用油箱隔板与床身窄间隙埋弧焊接为一体,床身更坚固,空间利用最大化。液压油箱内部需经酸洗磷化并保证内部清洁度达到NAS5-NAS6标准。
4.1.弯曲主轴,采用42CrMo合金钢材料,电渣二次重熔、锻造、两道热处理和研磨制作而成。主轴转动由两个德国FAG(或瑞典SKF)调心滚子轴承首尾支撑,从机头上部加热装配插入,装配精度和静、动刚度极高。弯曲作业时主轴可同时承受巨大径向力和轴向力带来的联合负载,主轴系可承受4倍弯曲臂额定工作时产生的倾覆力矩,主轴拥有极高的侧倾刚度,检查作业时的轴向和径向跳动近乎为零。弯曲轴总成安装在机头内部,为中空同心轴四层结构,由弯曲主轴、链轮传动系(含弯曲、复位油缸)、主模独立复位轴系、开合脱模工位,四部分组成,达到性能利用率最大化。
4.弯曲轴总成
该总成包含的轴系和工位:
A、主模复位
B、弯管工位
4.1.1.主轴法兰盘输出,采用定位销和防松螺钉与弯曲臂双面贴合接触连接,定位紧固并实时打表检测安装精度,高精度传递力矩更大,倾覆刚度更高。
4.1.2.主轴轴承,动载荷是工作额定载荷的四倍,精妙的轴盖设计既能防尘又能很好的储藏油脂,更近一步的提高了轴承寿命和精度保持性,额定作业状态下设计使用年限20年。
4.2.弯管链轮传动系(含弯曲、复位油缸),由弯曲和复位两支油缸浮动相互引拽链轮产生弯曲扭矩和往复运动,构成了高效、稳定、精准的弯曲传动方式。链轮采用42CrMo合金钢材料锻造经两道热处理和研磨制作而成,与弯曲主轴热装过盈配合更紧密,永不松动
4.2.1.为防止链条过载、冲击或因长时间作业疲劳而断裂,特采用大牌号双排短节距滚子链传递功率和扭矩,该链条可承受弯管油缸5倍额定引拽力。
4.2.2.弯曲油缸和复位油缸采用缸径与杆径比为2:1的大杆径结构具有极大的抗弯性,杆径内螺纹左右旋向连接链条,便于弯曲臂初始位置的精准调整和安装。
4.2.3.弯曲油缸和复位油缸采用浮动结构方式安装,在引拽链轮作业时,可消除链传动的多边形效应,同时利用系统背压相互作用自动涨紧链条,传动精确、平稳、可靠。避免了传统链板或单油缸引拽产生的啃轴现象和定期维护。
4.2.4.弯曲油缸和复位油缸构成的弯曲轴采用液压伺服比列阀数字化精准控制,智能电控(数控)系统实行曲线变载缓冲,精确定位弯曲臂的弯曲角度和复位精度,配合终端闭环检测或测量臂在线实时双向数据通讯检测和修正,使弯曲精度达到惊人的5弧分。
4.3.主模独立复位轴系,通过摆动油缸引拽链轮副回转。作业时,轴系与弯曲臂(内滑块)机械自锁传递扭矩同步弯曲,(90°)弯角作业完成后自锁解除,弯曲臂率先复位回零点,此时轴系静止保持(90°)弯角状态,待其他作业流程结束,轴系最后复位构成主模独立复位功能。该功能实现了弯管模和夹模在(90°)弯角作业后,有顺序的、依次回程复位,使连续弯曲作业能够顺利进行下一个环节或流程。避免了传统数控机床弯管模和夹模(弯曲臂)只能单一、同步的复位动作,在管材(90°)弯角作业后,因成品形状(角度)变得复杂,而引起的无法回程复位、卡死和干涉,避免小车二次(或更多次)停顿送料。
4.3.1.主模独立复位轴,加热或冷冻装配在弯曲主轴内,采用42CrMo合金钢材料锻造并经两道热处理和研磨制作而成,采用6个德国FAG(或瑞典SKF)滚子轴承首尾支撑,可承受4倍弯曲主模作业时产生的倾覆力矩,强大的侧倾刚度确保了作业时的回转同心精度和稳固性。
4.3.2.该轴系与平推式夹管工位和开合脱模工位,构成了机床在夹管、松开、连续弯管作业时的零干涉性能。
5.弯曲臂总成
弯曲臂总成与弯曲主轴上端面连接,传递扭矩。独创新颖的上中下三层结构,由弯曲臂箱体、平推式夹管工位和夹模半径调整工位三部分组成,张合托模油缸安装在该总成内,可拆卸式主模拉架安装在弯曲臂后端有利于薄壁小半径弯曲。
该总成包含的轴系和工位:
X101、夹紧工位
X102、夹模半径调整
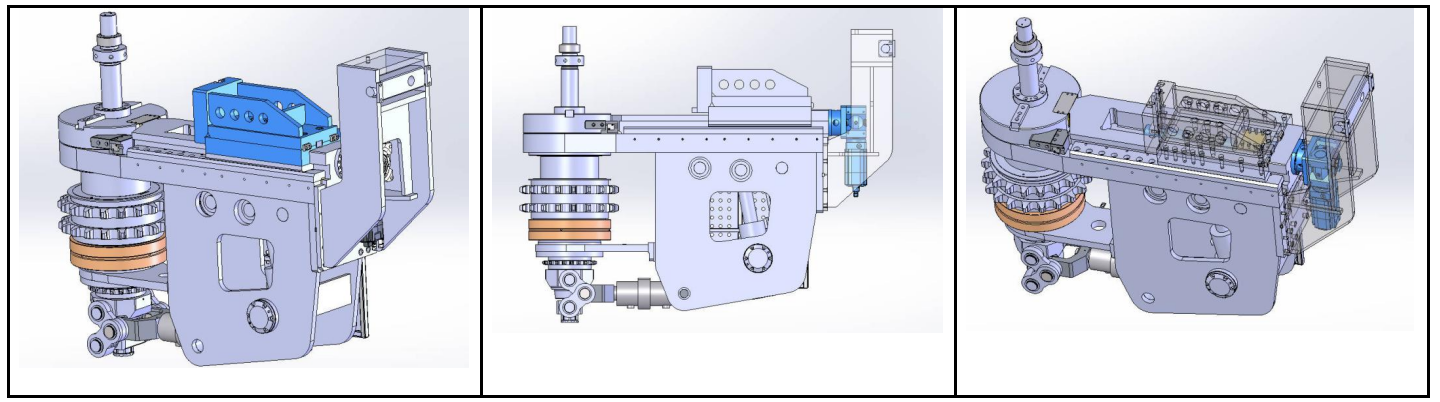
5.1. 弯曲臂箱体,结合有限元分析(FEM)和拓扑优化,加强筋纵横交错,采用高强度低合金板材加热焊接而成,并经退火消除内应力和抛丸处理,防永久性变形,机加工后经配研和铲刮工艺确保安装面贴合精度。
5.1.1. 弯曲臂箱体与弯曲主轴采用独创的法兰盘双面贴合紧固安装,为防止松动特采用销轴和防松螺钉连接紧固并实时打表检测安装精度,定位紧固精度稳定,传递力矩更大,倾覆刚度更高。箱体内的滑动面均镶嵌铝锡青铜并定时润滑,确保箱体无磨损。
5.1.2. 弯曲臂内侧安装有防夹人、物等急停碰撞防护板,设备的运动部位均有黄黑相间警示条。
5.1.3 床头底部安装有急停感应地毯,保证人工更换模具时的安全。
5.1.4. 人工操作设备本体易接触的危险部位贴有危险警告牌。
5.1.5. 弯曲臂通过销轴和螺栓固定在弯曲主轴上,由油缸驱动链条链轮带动主轴(弯曲臂)旋转,由编码器检测弯曲臂控制弯曲角度,弯曲臂可实现快速复位。油缸通过伺服比例阀控制,到达设定的角度前实行慢速缓冲、精准定位。
5.2. 平推式夹管工位,为内滑块,安装在弯曲臂箱体内,采用42CrMo合金钢材料整体锻造经两道热处理和研磨制作而成,由夹管油缸推进三连杆增力自锁机构使夹管工位滑块上的夹模做线性运动获得夹紧力,避免了需夹模半径调整工位的T型丝杆输出动载荷来夹管,夹紧力更大,三连杆增力自锁夹紧保持性更稳定。该工位避免了传统埋入式四连杆弧线升降夹管结构夹管作业时产生的搓管现象。
5.2.1. 平推式夹管工位与(A轴)主模独立复位轴系弯曲作业时机械自锁,保障了整机最高安全稳定性,该工位滑动面均镶嵌铝锡青铜并定时润滑延长寿命。
5.3. 夹模半径调整工位,自动控制、调节和定位夹模在不同半径模具状态下作业所需的位置。由绝对值伺服电机通过德国ALPHA原装进口直角精密行星减速机旋转驱动具有自锁特性的研磨级T型丝杆完成作业。无需人工复杂半径找位、对中和较准干预。
5.3.1. 夹模半径调整工位自动调节半径的功能,进一步扩大了弯曲多层模不同半径(差值、范围)作业的能力。
5.3.2. 夹模半径调整工位自动调节半径的功能,进一步扩大了夹模敞开行程,便于法兰管的法兰或变径管等特殊工艺管材顺利的从机床前部装卸料。
5.3.3. 用于控制调节和定位半径调整工位的研磨级T型丝杆,具有稳定的自锁特性。该丝杆巧妙的设计安装在平推式夹管工位的内部,避免了夹管作业需丝杆旋转输出动载荷而产生的磨损。
5.3.4. 该工位装配曲面型腔的夹紧模具,结合(A轴)主模独立复位功能,构成了整机杰出的零干涉性能可顺利将一根长管进行多角度、多维度、多个零直线段连续折弯而不干涉,实现“零直线段”的夹管连续弯制。
5.3.5. 绝对值伺服电机具有绝对测量和伺服零点驱动特性,能够数字化高精度执行 自动找位、对中作业,在断电重启、换模弯曲加工及模具更换时,无需人工复杂找位和较准干预。
5.3.6. 模块化设计,根据实际工况需求可在夹模半径调整工位上安装不同结构性能的夹模基座。
6.压料(辅推)总成
模块化设计,由有两个结构选项--平推直驱结构压料(辅推)总成和三连杆增力结构压料(辅推)总成,分别代表两种不同的性能特点,客户可根据实际工况需要,进行选装。
6.1. 平推直驱结构压料(辅推)模块由压料架、压料工位和独立的辅推装置三部分组成:
6.1.1.平推
直驱结构压料架,采用高强度低合金板材加热焊接而成,经有限元受力分析(FEM)和拓扑优化,加强筋纵横交错并经退火和抛丸处理消除内应力,防止作业受力时的震动和变形。
6.1.2.平推式压料工位,由压料油缸平推直驱辅推架实现作业,自动匹配半径和压紧力,无需人工干预。压料伺服油缸水平浮动安装在平推平推直驱结构压料架上。
6.1.2.1.制作多曲率半径模具,可实现不等R椭圆半径弯制。
6.1.3.独立的辅推模块,由独立的辅推工位安装在辅推架内
6.1.3.1.满足不同管径不同半径、不同管径同等半径、同等管径不同半径、多曲率半径、椭圆半径等特殊复杂的弯制需求,无需人工凭经验繁琐的调整。弯曲作业时,辅推可给与管件一定量的后推力,改善管件的外壁减薄率。
6.1.3.2.【特殊选项】预留辅推上下模块多用于汽车排气行业相同管径半径的多模连续作业。
6.2.【特殊选项】三连杆增力结构压料(辅推)总成,由三连杆增力压料架、三连杆增力压料工位和辅推顶镦模块三部分组成:6.2.1.三连杆增力结构压料架,采用高强度低合金板材加热焊接而成,经有限元受力分析(FEM)和拓扑优化,加强筋纵横交错并经退火和抛丸处理消除内应力,防止作业受力时的震动和变形。
6.2.2.三连杆增力压料工位,为内滑块,采用42CrMo合金钢材料整体锻造经两道热处理和研磨制作而成,由压料油缸驱动三连杆增力自锁机构使滑块工位实现线性运动,作业时夹紧力巨大。压料油缸垂直浮动安装在三连杆增力压料架上。
6.2.3.制作反变形槽导轨模具,利用三连杆增力压料工位巨大的压紧力,实现预变弯曲。
C、小车转角工位 X301、小车半径调整
Z301、小车前进工位 Z302、小车强推工位 Z303、小车夹管工位
7.1.小车抓管工位,与小车转角工位构成了精巧修长的炮筒结构,内外两层。抓管工位的炮筒,采用军工级合金钢经电渣二次重熔和热处理自紧工艺制作,内外两层伸缩夹管,避免了传统抓管动作由拨叉送料机构造成的抓管位移,稳定性和使用寿命较传统拨叉机构高出好几个量级(发明专利)。7.2.Detsch® 独创的大中孔内推式油缸,多台阶多瓣弧面精密弹性夹持装置(发明专利),最大程度的降低了夹管时的管材位移现象,同时满足不同规格的法兰管、套管(变径管)、直管及异型材的牢固夹持要求。
7.2.1.修长的炮筒伸出便于小车模块伸入机头区域(模具中心附近处)弯曲作业,极大有效的减少了对管材末段长度的要求,避免了管材浪费。
7.2.小车转角工位,与小车抓管工位结合构成炮筒结构,由伺服电机经德国原装进口ALPHA精密行星减速机驱动强劲的环面二次包络蜗轮蜗杆副实现空间立体转角作业,回转背隙小,精度高,传递扭矩和效率更高。
7.2.1.绝对值伺服电机具有绝对测量和伺服零点驱动特性,能够数字化高精度执行 自动找位、对中作业,在断电重启、换模弯曲加工及模具更换时,无需人工复杂找位和较准干预。
7.2.2.特殊附件--选装环形编码器实现闭环控制和检测,定位精度更高。强大的扭转力配合小车强推功能”可实现螺旋形状弯曲。
7.3.1.特殊附件--小车强推工位,是线性强力推进系统,作为小车送料定尺工位的强化延伸,由两个高性能恒功率绝对值伺服电机驱动两个德国ALPHA原装进口的强劲研磨级斜齿轮齿条机电一体线性系统 提供强劲的进给力,完成高精度大推力驱动和定位。该线性系统在弯曲作业时智能电控(数控、计算机)系统会自动匹配弯模半径产生的线速度数值和角度变换下的曲线推力数值,使之最大程度地减少弯曲臂拉应力带来的管外壁伤害,从而获得成品管外壁减薄的改善。双齿轮齿条强大的后推力也是实现推弯的核心条件,强大顶推力配合“小车转角工位”可实现螺旋形状弯曲【增配 绝对值测量系统 可确保更高精度和最低定位误差】。
7.3.2.特殊附件--绝对值测量系统,床身预留了磁栅尺或光栅尺的安装基础面,可安装测量系统实现全闭环控制来获得该工位“零回程间隙”超高精度驱动和定位。
7.4.小车半径调整工位,安装在送料工位上的两根大跨距重载滚柱线轨上,动滑静压复合导轨设计,使得强大的小车强推力仅作用在滑动硬轨上,极大的降低了线轨的负荷,从而使该工位具有超高的侧倾刚度,确保了在使用多层模具作业时仍具有很好的后推力来实现顶推助弯或大半径推弯。7.4.1.该工位采用绝对值伺服电机驱动德国ALPHA原装进口的强劲研磨级斜齿轮齿条机电一体线性系统,完成高精度驱动和定位,比传统的滚珠丝杆传动更耐冲击,更稳定,寿命更长。
7.4.2.自动调节位置对中模具弯曲半径,绝对值伺服电机零点驱动的特性能确保高精度和最低定位误差,在断电、开机重启和更换夹模时,无需人工再次复杂找位和较准干预,减少非作业时间极大地提高产能。
8.智能托料模块
伺服托料模块由滚动托辊、伺服托料升降工位、伺服位移定尺工位组成,安装在机身侧面,位置可移动。
8.1.滚动托辊采用尼龙(PA66)材料与加工的不锈钢管接触,避免管材污染、划伤。![]()
8.2.托料升降工位,均为伸缩式三层结构,互为抗倾覆力矩基础,垂直安装在位移定尺工位外侧。第一层伸缩板与位移定尺工位巧妙的设计为一体内部安装了齿条,采用2根滚柱重载线轨和四个滑块与第二层伸缩板连接(用于滑动),第二层伸缩板内部巧妙的设计安装了齿轮,同样采用2根滚柱重载线轨和四个滑块与第三层伸缩板连接(用于滑动)。
8.3.升降(伸缩)动作,由绝对值永磁同步伺服电机驱动德国ALPHA精密蜗轮蜗杆减速机齿轮齿条副完成。承重更大、响应速度更快、更耐冲击寿命更长。
8.4.升降(伸缩)传动件齿轮齿条副的2根滚柱重载线轨和四个滑块自身本可承载6倍工作托力,以确保该工位经久耐用20年。
8.5.位移定尺工位,均与小车模块一同安装在床身侧面的两根无拼接重载滚柱线轨上,分别安装在小车模块的前侧和后侧。采用绝对值永磁同步伺服电机驱动德国ALPHA强劲的线性系统(研磨级斜齿轮齿条和行星减速机一体化线性系统)获得额定位移力(自锁力)和最大位移速度,实现移动托料和定尺托料。
8.6.升降和位移定尺工位的绝对值伺服电机均具有绝对测量和伺服零点驱动特性,能够数字化高精度执行 依据不同作业管径和模具中心高度自动找位、上下对中,同时根据不同模具半径、弯曲速度和不同管件的加工长度自动调整跟随速度和托料位置(间距),极大的便利弯曲作业。
8.7.伺服托料模块在不作业时,自动收缩位移至侧推模块下方的非作业(安全)区域,主动让出行程,便利小车模块的炮筒能够伸入机头区域作业,极大有效的减少了弯曲作业对后段辅料长度的要求,避免管材浪费。
8.8.作业时无需人工再次复杂找位和较准干预。在断电重启、重新换模弯曲加工及模具更换时,无需人工复杂找位和较准干预,极大有效地减少了非作业时间。
9.抽芯模块
由半径调整工位、抽芯棒工位组成
该模块包含的轴系和工位:
X401、抽芯半径调整
Z401、抽芯棒工位
9.1.抽芯半径调整工位,安装在床身 上尾部的2根重载滚柱线轨上,线轨中心距大跨距具有极高的倾覆刚度,采用绝对值伺服电机驱动 德国ALPHA原装进口的强劲M4/cos19.5283°研磨级斜齿轮齿条机电一体线性系统,完成高高精度驱动和定位,比传统的滚珠丝杆传动更耐冲击,更稳定,寿命更长。
![]()
9.1.1.自动调节位置对中模具弯曲半径,绝对值伺服电机零点驱动的特性能确保高精度和最低定位误差,在断电、开机重启和更换芯棒时,无需人工再次复杂找位和较准干预,减少非作业时间,极大地提高产能。
9.1.2.采用无芯弯曲作业模式时,该工位自动调整抽芯模块位移至床身尾部最内侧的非作业安全区域,主动规避无芯弯曲长管材出现的碰撞和干涉,无需传统设备需要人工拆卸该模块。取消无芯弯曲工艺模式时,该工位自动复位并调整好作业半径,避免拆卸后的再次组装。
9.2.1.自润滑,弯管时可通过空心杆强压注油对插入管材内部的多球芯轴进行自动润滑,极大提高了芯轴寿命和弯头质量。
9.2.2.尾端活塞杆行程调节器,用来微调芯棒 插入管件内部位的位置达到最佳插芯弯管效果。
![]()
11.润滑装置
11.1.整机滑动面均镶嵌含带有润滑槽口的铝青铜。
11.2.脉冲控制的机电一体智能润滑系统,可预先设定供应剂量,借助分流器和高压塑料软管和毛细管将充足剂量的润滑油精确的输送到机床各个润滑点,确保整个传动系统在弯管机全寿命周期内具备超长使用寿命。
11.3.齿轮传动和链传动均通过聚氨脂泡沫(PU)制作的齿轮润滑,该泡沫齿轮还具有对传动齿面进行清洁的作用。
12.智能电控(数控)系统
采用基于Windows10 操作系统的德国原装进口工业计算机为上位机,通过多轴运动控制器对整机各功能模块、总成的轴系或工位实施极致性能的精确控制。该智能系统由人机交互系统(HMI)移动式操作界面(有启动及急停按钮),19寸投射式电容多点触摸、LCD彩色触摸屏、工业电脑(PC)和可编程多轴运动控制器(Motion controller PLC)、绝对值伺服驱动单元(servo)及电器柜五部分组成。
![]()
13.1.人机交互系统(HMI),5种沟通方式,使用者可根据不同作业环境和习惯来选择:
13.1.1.移动式触摸屏和一键操作
13.1.2.通讯接口传输和控制
13.1.3.互联网远程传输和控制
13.1.4.手持扫描枪扫码作业
13.1.5.测量臂在线检测和逆向应用
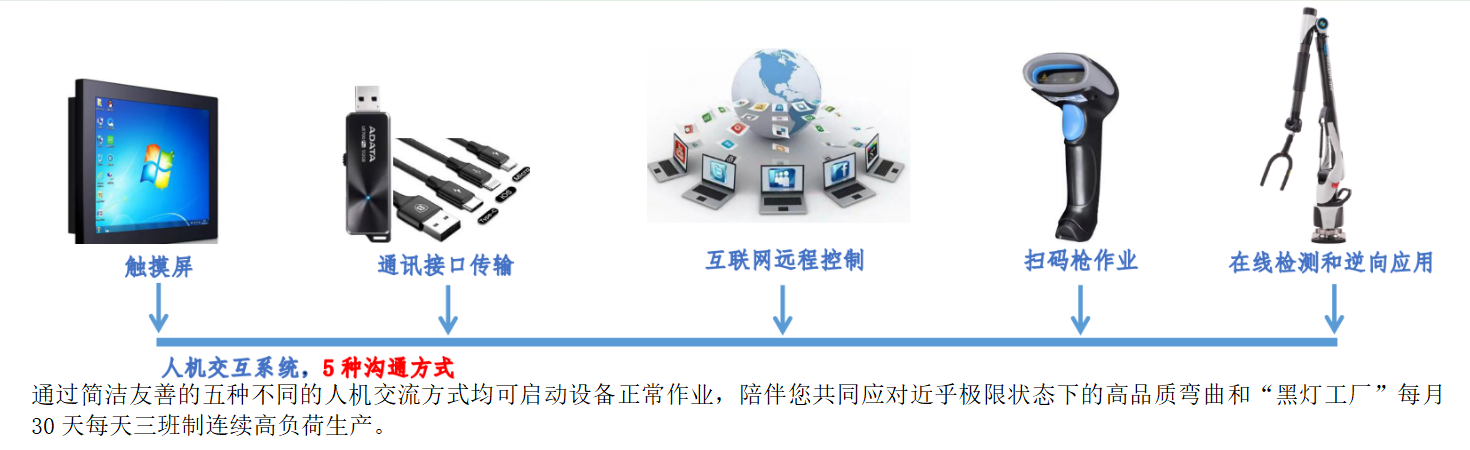
13.1.1.移动式操作界面(有启动及急停按钮),19寸投射式电容多点触摸、LCD彩色触摸屏,界面设计简洁易操作,有多个页面和窗口,可与键盘和鼠标连接,便于操作者实现下述功能作业;
13.1.1.1.可选择全自动、半自动、手动或脚踏四种操作模式进行弯曲加工作业。
13.1.1.2.可选择有芯、无芯、辅推顶镦和小车推弯四种工艺模式进行弯曲作业。
13.1.1.3.根据实际生产工况,可对各轴系和工位做速度和载荷的参数调整。
13.1.1.4.根据弯曲变化需求,可对各轴系和工位的作业顺序进行调整。
13.1.1.5.输入成品图纸X/Y/Z三坐标数值,触屏显示3D立体管件图形预览。
13.1.1.6.输入弯曲加工Y/B/C三坐标数值,触屏显示3D立体管件图形预览
13.1.1.7.一键转换功能--实现图纸X/Y/Z数值和Y/B/C加工数值相互转换。
13.1.1.8.一键转换功能--针对需要调头(反向)弯曲和对称管件弯曲,轻松获得转换后的数据和对称件镜像(射)数据,无需人为复杂计算和重新输入X/Y/Z或Y/B/C数值及程序编辑,给操作人员极大便利。
13.1.1.9.一键转换功能--计算工件的展开长度与下料长度,实现无余量下料。
13.1.1.10.动态三维模拟仿真,I/O检测、系统自动检测与错误提示。
13.1.2.通讯接口传输和控制,本人机交互系统,具有相当丰富的物理通讯接口,可以与打印机、扫描枪、测量臂等外部多个功设备连接,用于下载、无损传输和冗余操作,使之一机多用功能最大化。
13.1.2.1.USB3.1 TYPE-C数字信号接口,能同时传递音频和4K视频。
13.1.2.2.VGA模拟信号接口。
13.1.2.3.HDMI数字信号接口,能同时传递音频和视频信号。
13.1.2.4.DP1.4数字信号接口,能同时传递音频、视频及图像信号。
13.1.2.5.Profibus-DP现场总线接口,满足生产过程现场数据可存取性的要求,一方面覆盖了传感器/执行器领域的通讯要求,另一方面又具有单元级领域所有网络级通信功能。
13.1.2.6.Profinet基于以太网的现场,实施总线控制的工业通信协议。
13.1.2.7.EtherCat基于以太网的现场,实施总线控制的工业通信协议,特别在分散“I/O”领域,用途最广。
13.1.2.8.内存卡接口,2个。
13.1.3.互联网远程传输和控制,设计者可利用互联网或以太网将设计的3D立体三维管件模型或参数以step、 igs、 excel、word、 txt等格式传输至弯管机,实现远程图形传输并获取坐标值(X/Y/Z、Y/B/C)。
13.1.3.1设计者亦可通过工业计算机丰富的扩展接口USB、HDMI、Profibus-DP、Profinet、Ethernet、VGA与触控显示屏连接,实现低时延人机交互。设备能接收单个或多个弯管数控指令(mes、csv、xml等格式),进行批量自动弯管。数控设备系统,开放数据访问权限,便于其他应用系统集成。
13.1.3.2.弯管机PC可自动读取文件或图纸并生成加工程序和加工参数,实现远程自动弯管作业,具备离线、在线批量导入数据功能,减少或杜绝手动录入加工参数,弯曲结束后设备进行反馈,实现无人干预自动作业。
13.1.4.手持扫描枪(QR code)可扫描读取管件上的二维码或标签,自动调用与二维码或标签相对应的各个管件参数并生成加工程序和加工数值。
13.1.4.1.扫描读取同时,17寸彩屏显示3D管件图形预览,便于操作者观察,实现扫描自动作业。
13.1.4.2.管件设计者提前做生产排程--编辑和设定管件与二维码或标签相对应的参数并设定好需要加工的程序和数量,是实现本性能的必要条件。
13.1.5.测量臂在线检测和逆向应用,德系重工科技有限公司与瑞典HEXAGON集团公司战略合作,采用海克斯康集团公司全新推出的RA73系列柔性测量系统与detsch®弯管机通讯协议互联互通并可TCP/IP数据共享和U盘拷贝共享。RA73测量臂为移动式非接触三坐标,具备多种激光扫描头,可自由搭配使用随时随地对不同外径的圆管、方管、矩形管及异型材的弯曲成品进行现场检测。
13.1.5.1.在线测量--扫描各弯曲点,测量臂自行识别和分析检测弯曲轴线、弯曲点和其他弯曲元素的变化并精确的采集实际数据反馈给计算机,计算机将测量臂扫描采集来的实际数据直接与数据库补偿值比对并及时修正传达给弯管机按照修正后的补偿值执行弯曲作业,以此确保最低管件成品误差。
13.1.5.1.1.测量臂在履行“在线测量”各项检测任务的过程中与计算机系统实时双向数据通讯,以便计算机系统能够快速的传达新的修正补偿值给弯管机执行弯曲作业,达到快速消除或抑制弯曲误差积累的目的。
13.1.5.2.逆向工程系统应用,在样品管件没有3D数模和图纸的情况下,利用测量臂扫描样品管件获取样品坐标参数(X/Y/Z/A/B/C)并自行生成3D数模和CAD数模。
13.1.5.2.1可连接打印机打印该样品图纸,也可通过TCP/IP数据共享或U盘拷贝与其他设备共享该文件。